דיקט עשוי משלוש שכבות דקות או יותר של עץ המודבקות יחד באמצעות דבק. כל שכבת עץ, או דיקט, בדרך כלל מכוונת כך שסיביה נמצאים בזווית ישרה לשכבה הסמוכה על מנת להפחית את ההתכווצות ולשפר את חוזק החתיכה המוגמרת. רוב הדיקט נדחס ליריעות גדולות ושטוחות המשמשות בבניית מבנים. חתיכות דיקט אחרות עשויות להיות מעוצבות לעקומות פשוטות או מורכבות לשימוש ברהיטים, סירות ומטוסים.
השימוש בשכבות דקות של עץ כאמצעי בנייה מתוארך לסביבות שנת 1500 לפני הספירה, כאשר אומנים מצרים הדביקו חתיכות דקות של עץ אבוני כהה לחלק החיצוני של ארון ארז שנמצא בקברו של המלך תות-אנח-אמן. טכניקה זו שימשה מאוחר יותר את היוונים והרומאים לייצור רהיטים יוקרתיים וחפצי נוי אחרים. במאה ה-17, אמנות עיטור הרהיטים עם חתיכות עץ דקות נודעה בשם ציפוי, והחתיכות עצמן נודעו בשם ציפוי.
עד סוף המאה ה-18, חתיכות הפורניר נחתכו לחלוטין ביד. בשנת 1797, הגיש האנגלי סר סמואל בנת'ם בקשה לפטנטים המכסים מספר מכונות לייצור פורנירים. בבקשות הפטנט שלו, הוא תיאר את הרעיון של למינציה של מספר שכבות של פורניר עם דבק ליצירת חתיכה עבה יותר - התיאור הראשון של מה שאנו מכנים כיום דיקט.
למרות התפתחות זו, נדרשו כמעט מאה שנים נוספות עד שציפויי למינציה מצאו שימושים מסחריים מחוץ לתעשיית הרהיטים. בסביבות שנת 1890, עץ למינציה שימש לראשונה לבניית דלתות. ככל שהביקוש גדל, מספר חברות החלו לייצר יריעות עץ למינציה מרובות שכבתיות, לא רק לדלתות, אלא גם לשימוש בקרונות רכבת, אוטובוסים ומטוסים. למרות השימוש הגובר, הרעיון של שימוש ב"עץ מודבק", כפי שקראו לו כמה אומנים בסרקזם, יצר תדמית שלילית למוצר. כדי להתמודד עם תדמית זו, יצרני עץ הלמינציה נפגשו ולבסוף החליטו על המונח "דיקט" כדי לתאר את החומר החדש.
בשנת 1928 הוצגו בארצות הברית לוחות הדיקט הראשונים בגודל סטנדרטי של 1.2 מטר על 2.4 מטר (4 רגל על 8 רגל) לשימוש כחומר בנייה כללי. בעשורים שלאחר מכן, דבקים משופרים ושיטות ייצור חדשות אפשרו שימוש בדיקט למגוון רחב של יישומים. כיום, דיקט החליף את העץ החתוך למטרות בנייה רבות, וייצור דיקט הפך לתעשייה עולמית של מיליארדי דולרים.
השכבות החיצוניות של דיקט ידועות בהתאמה כ"פאה" ו"גב". ה"פאה" היא המשטח שיש להשתמש בו או לראותו, בעוד שהגב נותר ללא שימוש או מוסתר. השכבה המרכזית ידועה כליבה. בדיקטים עם חמש שכבות או יותר, השכבות הביניים ידועות כ"פסים צולבים".
דיקט יכול להיות עשוי מעצים קשה, עצים רכים, או שילוב של השניים. כמה עצים קשים נפוצים כוללים אפר, מייפל, מהגוני, אלון וטיק. העץ הרך הנפוץ ביותר המשמש לייצור דיקט בארצות הברית הוא אשוח דאגלס, אם כי משתמשים גם בכמה זנים של אורן, ארז, אשוח וסקויה.
דיקט מרוכב מורכב מלוח חלקיקים או מחתיכות עץ מלא המחוברות קצה לקצה. הוא מגומר בציפוי דיקט בצד ובגב. דיקט מרוכב משמש במקומות בהם נדרשות יריעות עבות מאוד.
סוג הדבק המשמש לחיבור שכבות העץ יחד תלוי ביישום הספציפי של הדיקט המוגמר. יריעות דיקט מעץ רך המיועדות להתקנה על החלק החיצוני של מבנה משתמשות בדרך כלל בשרף פנול-פורמלדהיד כדבק בגלל חוזקו המעולה ועמידותו בפני לחות. יריעות דיקט מעץ רך המיועדות להתקנה על החלק הפנימי של מבנה עשויות להשתמש בדבק חלבון דם או חלבון סויה, אם כי רוב יריעות העץ הרך הפנימיות עשויות כיום מאותו שרף פנול-פורמלדהיד המשמש ליריעות חיצוניות. דיקט קשה המשמש ליישומים פנימיים ולבניית רהיטים עשוי בדרך כלל משרף אוריאה-פורמלדהיד.
יישומים מסוימים דורשים יריעות דיקט בעלות שכבה דקה של פלסטיק, מתכת, או נייר או בד ספוגים בשרף המודבקים לפנים או לגב (או לשניהם) כדי להעניק למשטח החיצוני עמידות נוספת בפני לחות ושחיקה או כדי לשפר את תכונות אחיזת הצבע שלו. דיקט כזה נקרא דיקט חצוי והוא משמש בדרך כלל בתעשיות הבנייה, התחבורה והחקלאות.
יריעות דיקט אחרות עשויות להיות מצופות בצבע נוזלי כדי להעניק למשטחים מראה מוגמר, או שניתן לטפל בהן בכימיקלים שונים כדי לשפר את עמידות הדיקט בפני להבה או ריקבון.
ישנם שני סוגים רחבים של דיקט, לכל אחד מערכת דירוג משלו.
סוג אחד ידוע כבנייה ותעשייה. דיקט מסוג זה משמש בעיקר בשל חוזקו ומדורג לפי יכולת החשיפה שלו ודרגת הציפוי בו משתמשים על הפנים והגב. יכולת החשיפה יכולה להיות פנימית או חיצונית, בהתאם לסוג הדבק. דרגות ציפוי יכולות להיות N, A, B, C או D. דרגה N בעלת מעט מאוד פגמים על פני השטח, בעוד שדרגה D עשויה להיות בעלת קשרים וסדקים רבים. לדוגמה, דיקט המשמש לריצוף משנה בבית מדורג כ-"פנימי CD". משמעות הדבר היא שיש לו פנים C עם גב D, והדבק מתאים לשימוש במקומות מוגנים. השכבות הפנימיות של כל דיקט הבנייה והתעשייה עשויות מציפוי דרגה C או D, ללא קשר לדירוג.
סוג אחר של דיקט ידוע כעץ קשה ודקורטיבי. דיקטים מסוג זה משמשים בעיקר בשל המראה שלהם ומדורגים בסדר יורד של עמידות בפני לחות כטכני (חיצוני), סוג I (חיצוני), סוג II (פנימי) וסוג III (פנימי). ציפויי הפנים שלהם כמעט נקיים מפגמים.
גדלים
עובי יריעות דיקט נע בין 1.6 מ"מ (0.06 אינץ') ל-76 מ"מ (3.0 אינץ'). העוביים הנפוצים ביותר הם בטווח של 6.4 מ"מ (0.25 אינץ') עד 19.0 מ"מ (0.75 אינץ'). למרות שהליבה, הפסים הצולבים, והצד הקדמי והאחורי של יריעת דיקט עשויים להיות עשויים פורנירים בעוביים שונים, עובי כל אחד מהם חייב להיות מאוזן סביב המרכז. לדוגמה, הצד הקדמי והאחורי חייבים להיות בעובי שווה. כמו כן, הפסים הצולבים העליונים והתחתונים חייבים להיות שווים.
הגודל הנפוץ ביותר של לוחות דיקט המשמשים בבניית מבנים הוא רוחב 1.2 מטר (4 רגל) ואורך 2.4 מטר (8 רגל). רוחבים נפוצים אחרים הם 0.9 מטר (3 רגל) ו-1.5 מטר (5 רגל). האורכים נעים בין 2.4 מטר (8 רגל) ל-3.6 מטר (12 רגל) במרווחים של 0.3 מטר (1 רגל). יישומים מיוחדים כמו בניית סירות עשויים לדרוש לוחות גדולים יותר.
העצים המשמשים לייצור דיקט הם בדרך כלל קטנים יותר בקוטר מאלה המשמשים לייצור עץ. ברוב המקרים, הם ניטעו וגודלו באזורים שבבעלות חברת דיקט. אזורים אלה מנוהלים בקפידה כדי למקסם את צמיחת העצים ולמזער נזקים מחרקים או אש.
להלן רצף פעולות טיפוסי לעיבוד עצים ללוחות דיקט סטנדרטיים בגודל 1.2 מטר על 2.4 מטר (4 רגל על 8 רגל):
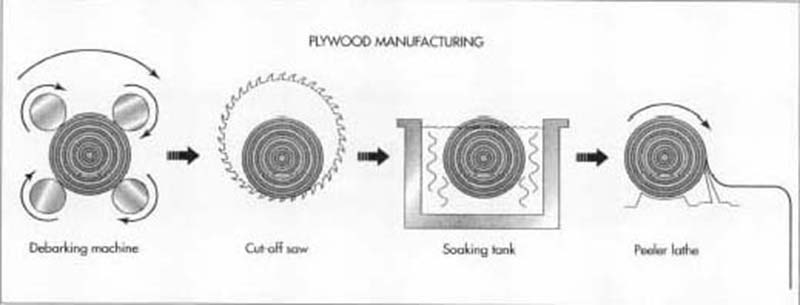
תחילה מסירים את קליפת הגזעים ולאחר מכן נחתכים לגושים לקילוף. על מנת לחתוך את הגושים לרצועות של פורניר, הם מושרים תחילה ולאחר מכן מקולפים לרצועות.
1 עצים נבחרים באזור מסומנים כמוכנים לכריתה או לכריתה. הכריתה יכולה להתבצע באמצעות מסורי שרשרת המונעים בבנזין או באמצעות מספריים הידראוליות גדולות המותקנות על חזית כלי רכב בעלי גלגלים הנקראות כריתות עצים. הענפים מוסרים מהעצים שנפלו באמצעות מסורי שרשרת.
2 גזעי העצים הגזומים, או בולי העץ, נגררים לאזור טעינה על ידי כלי רכב בעלי גלגלים הנקראים מחליקים. בולי העץ נחתכים לאורך ומועמסים על משאיות לקראת הנסיעה למפעל דיקט, שם הם נערמים בערימות ארוכות המכונות סיפוני בולי עץ.
3 כאשר יש צורך בבול עץ, הוא נאסף מסיפוני העץ על ידי מעמיסים בעלי צמיגי גומי ומונח על מסוע שרשרת המוביל אותם למכונת הסרת הקליפה. מכונה זו מסירה את הקליפה, באמצעות גלגלי השחזה בעלי שיניים חדות או באמצעות סילוני מים בלחץ גבוה, בעוד בול העץ מסובב באיטיות סביב צירו הארוך.
4 בולי העץ המנוקים מקליפות העץ מועברים למנסרה על מסוע שרשרת, שם מסור עגול ענק חותך אותם לחתיכות באורך של כ-2.5 מטר עד 2.6 מטר, המתאים לייצור יריעות סטנדרטיות באורך 2.4 מטר. חתיכות בולי עץ אלה ידועות כבלוקי קילוף.
5 לפני שניתן לחתוך את הציפוי, יש לחמם ולהשרות את בלוקי הקילוף כדי לרכך את העץ. ניתן לאדות את הבלוקים או לטבול אותם במים חמים. תהליך זה אורך 12-40 שעות, תלוי בסוג העץ, בקוטר הבלוק וגורמים נוספים.
6. בלוקי הקילוף המחוממים מועברים לאחר מכן למחרטת הקילוף, שם הם מיושרים אוטומטית ומוזנים למחרטה אחד בכל פעם. כאשר המחרטה מסובבת את הבלוק במהירות סביב צירו הארוך, להב סכין באורך מלא מקלף יריעת פורניר רציפה מפני השטח של הבלוק המסתובב בקצב של 90-240 מטר לדקה (300-800 רגל לדקה). כאשר קוטר הבלוק מצטמצם לכ-230-305 מ"מ (3-4 אינץ'), פיסת העץ הנותרת, המכונה ליבת הקילוף, נפלטה מהמחרטה ובלוק קילוף חדש מוזן למקומו.
7 ניתן לעבד את יריעת הפורניר הארוכה היוצאת ממחרטת הקולפן/מחרטה באופן מיידי, או לאחסנה במגשים ארוכים מרובי מפלסים או ללפף אותה על גלילים. בכל מקרה, התהליך הבא כרוך בחיתוך הפורניר לרוחבים שמישים, בדרך כלל כ-1.4 מטר (4 רגל-6 אינץ'), לייצור יריעות דיקט סטנדרטיות ברוחב 1.2 מטר (4 רגל). במקביל, סורקים אופטיים מחפשים קטעים עם פגמים בלתי מקובלים, ואלה נחתכים, ומשאירים חתיכות פורניר ברוחב קטן מהסטנדרטי.
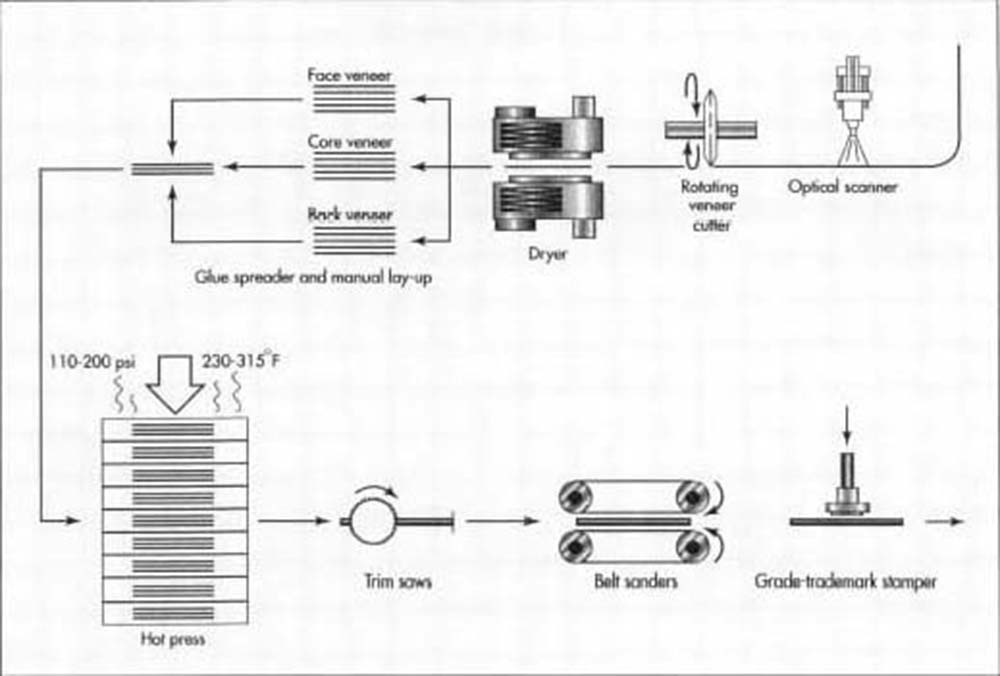
רצועות הפורניר הרטובות מלופפות לגליל, בעוד סורק אופטי מזהה פגמים בלתי מקובלים בעץ. לאחר הייבוש, הפורניר מדורג ונערם. חלקים נבחרים של פורניר מודבקים יחד. מכבש חם משמש לאיטום הפורניר לחתיכת דיקט אחת מוצקה, אשר תעבור גזירה ושיוף לפני הטבעה בדרגה המתאימה.
8. לאחר מכן, ממוינים ונערמים חתיכות הציפוי לפי דרגה. ניתן לעשות זאת באופן ידני, או באופן אוטומטי באמצעות סורקים אופטיים.
9 החלקים הממוינים מוזנים למייבש כדי להפחית את תכולת הלחות שלהם ולאפשר להם להתכווץ לפני הדבקתם יחד. רוב מפעלי הדיקט משתמשים במייבש מכני שבו החלקים נעים ברציפות דרך תא מחומם. בחלק מהמייבשים, סילוני אוויר מחומם במהירות גבוהה מוספים על פני החלקים כדי להאיץ את תהליך הייבוש.
10 כאשר חלקי הציפוי יוצאים מהמייבש, הם נערמים לפי דרגה. לחלקים התחתונים יש ציפוי נוסף המודבק באמצעות סרט דביק או דבק כדי להפוך את החלקים מתאימים לשימוש בשכבות הפנימיות שבהן המראה והחוזק פחות חשובים.
11 קטעי הציפוי שיותקנו לרוחב - הליבה ביריעות בנות שלוש שכבות, או הפסים הצולבים ביריעות בנות חמש שכבות - נחתכים לאורכים של כ-1.3 מטר (4 רגל-3 אינץ').
12 כאשר מורכבים חלקי הציפוי המתאימים עבור רצף מסוים של דיקט, מתחיל תהליך הנחת והדבקת החלקים יחד. ניתן לעשות זאת באופן ידני או חצי אוטומטי באמצעות מכונות. במקרה הפשוט ביותר של יריעות בעלות שלוש שכבות, הציפוי האחורי מונח שטוח ומועבר דרך מפזר דבק, אשר מורח שכבת דבק על המשטח העליון. לאחר מכן, החלקים הקצרים של ציפוי הליבה מונחים לרוחב על גבי הגב המודבק, וכל היריעה עוברת דרך מפזר הדבק בפעם השנייה. לבסוף, הציפוי הקדמי מונח על גבי הליבה המודבקת, והיריעה נערמת עם יריעות אחרות הממתינות להיכנס למכבש.
13 היריעות המודבקות נטענות לתוך מכבש חם בעל מספר פתחים. מכונות הדפוס יכולות לטפל ב-20-40 יריעות בו זמנית, כאשר כל יריעת נטענת בחריץ נפרד. לאחר טעינת כל היריעות, המכבש לוחץ אותן יחד תחת לחץ של כ-7.6-13.8 בר (110-200 psi), ובמקביל מחמם אותן לטמפרטורה של כ-109.9-157.2 מעלות צלזיוס (230-315° פרנהייט). הלחץ מבטיח מגע טוב בין שכבות הציפוי, והחום גורם לדבק להתקשות כראוי לחוזק מקסימלי. לאחר פרק זמן של 2-7 דקות, המכבש נפתח והיריעות נפרקות.
14 הלוחות המחוספסים עוברים דרך סט של מסורים, אשר גוזמים אותם לרוחב ולאורכם הסופיים. לוחות בדרגה גבוהה יותר עוברים דרך סט של מלטשות רצועות ברוחב 1.2 מטר (4 רגל), אשר משייפות גם את הפנים וגם את הגב. לוחות בדרגה בינונית משוייפים ידנית נקודתית כדי לנקות אזורים מחוספסים. חלק מהלוחות עוברים דרך סט של להבי מסור עגול, אשר חותכים חריצים רדודים בפנים כדי להעניק לדיקט מראה מחוספס. לאחר בדיקה סופית, כל הפגם שנותר מתוקן.
15 היריעות המוגמרות מוטבעות בסימן מסחרי של דרגה המספק לקונה מידע על דירוג החשיפה, הדרגה, מספר המפעל וגורמים נוספים. יריעות מאותו דרגה מחוברות יחד בערימות ומועברות למחסן להמתנה למשלוח.
בדיוק כמו עם עץ, אין דבר כזה חתיכת דיקט מושלמת. לכל חתיכות הדיקט יש כמות מסוימת של פגמים. מספרם ומיקום הפגמים הללו קובעים את דירוג הדיקט. תקנים לדיקט לבנייה ולתעשייה מוגדרים על ידי תקן המוצר PS1 שהוכן על ידי הלשכה הלאומית לתקנים ואיגוד הדיקט האמריקאי. תקנים לדיקט קשה ולדיקט דקורטיבי מוגדרים על ידי ANSIIHPMA HP שהוכן על ידי מכון התקנים הלאומי האמריקאי ואיגוד יצרני דיקט קשה. תקנים אלה לא רק קובעים את מערכות הדירוג לדיקט, אלא גם מפרטים קריטריונים לבנייה, ביצועים ויישום.
למרות שדיקט עושה שימוש יעיל למדי בעצים - למעשה פירוקם והרכבתם מחדש לתצורה חזקה ושימושית יותר - עדיין ישנה בזבוז ניכר הטמון בתהליך הייצור. ברוב המקרים, רק כ-50-75% מנפח העץ השמיש בעץ מומר לדיקט. כדי לשפר נתון זה, מספר מוצרים חדשים נמצאים בפיתוח.
מוצר חדש אחד נקרא לוח גדילי אוריינטציה (oriented strand board), המיוצר על ידי גריעת בול העץ כולו לגדילים, במקום קילוף ציפוי מהבול והשלכת הליבה. הגדילים מעורבבים עם דבק ונדחסים לשכבות כאשר הסיבים זורמים בכיוון אחד. לאחר מכן, שכבות דחוסות אלו מכוונות בזווית ישרה זו לזו, כמו דיקט, ומודבקות יחד. לוח גדילי אוריינטציה חזק כמו דיקט ועולה מעט פחות.
זמן פרסום: 10 באוגוסט 2021